Understanding Rust in Solenoid Valves
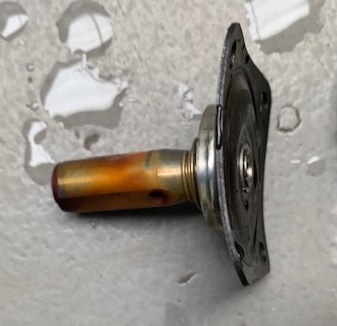
Rust in solenoid valves can lead to operational failures, especially when the valve remains energized for extended periods. This condition can cause the valve to stick in the open position, leading to coil overheating and potential burnout, particularly in AC 50/60Hz systems.
A common misconception is mistaking sulphide blooms for rust. Valves made from 303 stainless steel, known for its high sulphur content, may exhibit surface discolouration due to sulphide exposure to moisture. To differentiate, soak the affected part in a 10% sodium hydroxide (NaOH) solution overnight. If the discolouration wipes away without leaving pitting, it's likely sulphides, not rust.
Common Causes of Rust Formation in a solenoid valve
Material Composition: Using 303 stainless steel, which contains high sulphur, can lead to sulphide blooms that mimic rust.
Water Quality: Mains water supplies can carry rust particles, especially in older or corroded pipelines.
Installation Debris: Metal shavings from cutting or threading pipes during installation can remain in the system, leading to rust accumulation.
Chemical Exposure: Introducing concentrated cleaning chemicals into new pipework without proper dilution can cause corrosion, especially in stagnant areas like solenoid core tubes.
Preventative Measures
Material Selection: Opt for solenoid valves made from corrosion-resistant materials like 316 stainless steel, which offers better resistance to chlorides and other corrosive agents.
Proper Cleaning: Before installation, thoroughly clean pipework to remove any metal debris. Avoid using undiluted cleaning agents; instead, dilute chemicals appropriately and flush the system with clean water.
Magnetic Descale Units: Installing magnetic descalers upstream can capture rust particles, preventing them from entering the solenoid valve.
Regular Maintenance: Implement a maintenance schedule to inspect, clean and repair solenoid valves, ensuring they operate efficiently and prolonging their lifespan.
Addressing Water Hardness
Hard water, measured above 20-25 French degrees, can lead to scale build-up in solenoid valves. To mitigate this:
Water Softening Systems: Install systems to reduce water hardness, preventing scale accumulation.
Functional Consideration: Use solenoid valves with bi-stable latching function for reduced heat buildup, or consider actuated ball valves for better resistance to scaling.
Maintenance Tips
Routine Inspections: Regularly check for signs of rust or scale build-up.
Cleaning Protocols: Use appropriate cleaning agents for different valve components. For instance, isopropyl alcohol is suitable for metal parts, while mild detergents work for plastic and rubber components.
Operational Checks: Ensure valves return to their fail-safe positions promptly when de-energised.
Conclusion
Rust in solenoid valves can compromise system efficiency and safety. By understanding the causes and implementing preventive measures, you can ensure the longevity and reliability of your solenoid valves. Regular maintenance, proper material selection, and addressing water quality issues are key to preventing rust-related problems.
For more detailed information and product selections, please contact us.