Valve Fault-finding guide
Read our Frequently Asked Questions
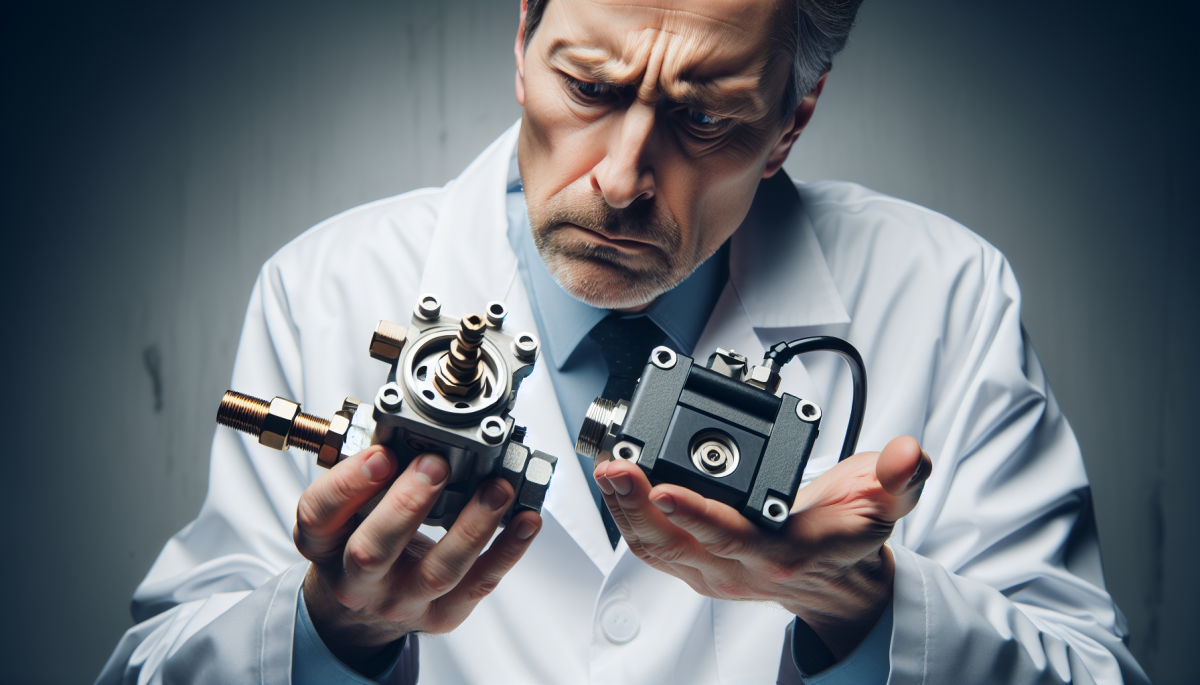
Solenoid valve fault-finding guide.
At some point in their life, a solenoid valve will fail and stop working.
The reasons for valve failure and vast and varied from dirt ingress, damage, worn out, maintenance mistakes or simply the solenoid valve is not suited to the application at hand.
Some initial key pointers before you start troubleshooting here are:
If the valve never worked.
This might indicate that the valve is not suited for the application. i.e. wrong pressure, type or voltage etc, was installed incorrectly or was damaged.
Check all specifications with your solenoid valve supplier.
If the valve was working before
This might indicate that either some system changes have affected the valve, or debris has become lodged inside, so some simple valve maintenance will bring the valve back online and working correctly.
Check with your solenoid valve supplier before purchasing any spare parts, solenoid seals or solenoid coils.
Solenoid Valve only opens slightly
Dirt ingress under the diaphragm
Clean diaphragm / piston seals or replace if damaged. See spare parts list, maybe fit Y type strainer upstream.
Low pressure
Check inlet/ outlet pressure difference (Differential) is in line with valve specification. If too low, the valve will need replacing with 0 rated version. Remember that the downstream outlet side pressure will rise, especially if the outlet pipework rises vertically to a tank, is restricted by another valve or the pipe reduces in size.
If so the outlet pressure downstream is subtracted from the supply side pressure upstream to calculate the pressure difference or differential. Other system demands may also reduce the overall supply pressure and further reduce differential pressure.
Damaged or bent armature tube
Replace tube. See spare parts.
Corrosion
Replace damaged components and check media compatibility of the valve and seal material.
See our chemical compatibility charts.
Do not use EPDM seals on Oils or Fats as the seals will swell and restrict flow.
Call our technical help line or soak seals overnight to see if seal swells up
Missing components after maintenance
Replace parts according to the spares listing. Solenoid seals and armatures.
Solenoid Valve fails to open
Failed power supply
Check if valve is normally closed (Power to open) Or Normally Open (Power to close) Use magnetic detector lift coil slightly to check if magnetic field is present.
Do not remove coil if energised as IT WILL BURN OUT
Check contacts Check wire connections and DIN connector.
Check fuses.
Wrong Voltage
Check coil marked voltage is correct for supply.
Check voltage tolerances normally +/- 10% however refer to solenoid valve data sheet.
Some AC (alternating Current) coils work on the principle of creating an inrush condition to open the valve, check your power supply is rated for the coil current requirements.
Most valves will have cable plugs rated to IP65, ensure cable gland and cable diameter are matched, plug connecting screw correctly tightened and allow cable to drop under cable gland to help prevent ingress of water droplets.
Coil burnt out
See coil burnt section
Pressure Too High
Check coil power rating, higher power version may be required. Reduce inlet pressure in line with valve specification as shown in solenoid valve data sheet.
Pressure Too Low
Check inlet/ outlet pressure difference (Differential) is in line with design conditions of the valve.
If too low valve will need replacing with 0 rated assisted lift version.
Remember that the downstream pressure will rise with vertical pipework, other control equipment or systems.
The outlet pressure should be deducted from the inlet supply pressure to give the pressure difference or differential, andother system demands from the inlet may also reduce the overall supply pressure and further reduce pressure differentials.
Damaged Armature tube
Replace armature tube. See spare parts list.
Dirt ingress in armature tube
Clean valve armature or replace. Suspended particles of dirt can be filtered out with a filter strainer, always mount valve with coil upright to reduce wear on the top of the solenoid armature if any dirt gets into the medium. If hard water scale builds up; install water softener or install a motor actuated ball valve, otherwise install Y type strainer to filter out suspended particles.
Corrosion
Replace damaged components and check media compatibility with valve. See our chemical compatibility charts.
If the armature is pitted due to cleaning or dosing fluid? Some acids will attack the 430F stainless armature, which is corrosion resistant but not guaranteed to withstand all fluids.
Missing components after maintenance
Replace parts according to spares listing.
Solenoid valve fails to close or partly closes
Dirt ingress under diaphragm or piston seals.
Clean diaphragm or piston seals and remove any debris. Fit filter upstream to prevent debris entering valve.
Residual power to coil
Lift the coil slightly to check if magnetic field is present. Do not completely remove the coil if energised as IT WILL BURN OUT.
Check wiring diagram, Check lead connections.
Dirt ingress in pilot hole under coil armature
Clean orifice with pin or compressed air.
Manual override
Check position of manual override and adjust if required.
Pressure pulse upstream.
Check valve technical data for the solenoid valve and replace if necessary.
Pressure difference in/out too high
Check pressure and flow
Outlet pressure occasionally higher than inlet pressure fit check or motor actuated ball valve
Check other items in installation.
Damaged or bent armature tube
Replace tube. See spare parts for solenoid valve.
Diaphragm inverted
Refit diaphragm correctly or replace with new part. See valve seal and spares.
Dirt ingress in armature tube
Clean valve armature or replace. If hard water scale build up, install water softener or motor ball valve.
Corrosion in pilot orifice
Replace damaged components, check valve specification in suitable for application.
Valve installed wrong way around
Check flow direction is in line with flow direction arrow or in/out markings on ports.
Missing components after maintenance
Replace parts according to spares listing.
Water Hammer Fault Finding
Valve Noise Appears Incorrect
Armature cannot reach top due to over pressure or debris.
Check armature tube and armature assembly for debris and clean or replace accordingly.
Check system pressure is in accordance with valve specification. Reduce system pressure.
Solenoid valve noisey "Buzzing" 50 or 60Hz AC buzz. Use DC solenoid coil with DC supply or fit bridge rectified connector to convert AC supply to DC for new DC solenoid coil.
Water hammer when valve opens
Caused by high liquid velocity and high pressure through small pipe bore.
Install a closed vertical T piece pipe in before the valve to trap an air pocket to dampen noise.
Reduce inlet pressure.
Increase pipe size to reduce velocity.
Install slow closing, anti water hammer WRAS solenoid valve or actuated ball valve.
Install motor actuated ball valve.
Water hammer when valve closes
Caused by high liquid velocity and high pressure through small pipe bore. Ask supplier to reduce closing time of valve. This can be done carefully by increasing slightly (10-20%) the size of the pilot pressure equalising hole in the diaphragm. Too much and valve will not open.
Reduce inlet pressure
Increase pipe size to reduce velocity.
Install slow closing WRAS water solenoid valve.
Coil Armature Slow
Replace damaged armature, see spares section.
Check media compatibility with valve.
Bent armature tube, replace accordingly.
Dirt in armature tube, clean and fit Y type strainer.
Coil Burnt / Melted or Cold with Power On
Check coil marked voltage is correct with power supply. Change coil for correct one if required.
Check wiring and wiring diagram
Check voltage tolerance, normally +/- 10% consult solenoid valve catalogue.
Coil Short Circuit
Check remaining installation for short circuit Check lead connections at coil and DIN connector
Check for moisture in coil, replace as required.
According to the laws of physics current can only flow in a closed circuit, if this is interrupted that current can no longer flow. So a burnt coil is open circuit - no current.
Check coil IP rating according to technical data in solenoid valve catalogue
Media Temperature Too High
Check media temperature against valve technical data in solenoid-valve catalogue. Move valve to cooler area or increase ventilation around valve & coil. Find high temperature valves
Check you have correct function normally closed or normally open.
WRAS water solenoid valves 0.5-3 Sec Open + Close anti water hammer design.
WRAS Motor Actuated Ball Valves 5 Sec Open + Close anti water hammer design.
Motor actuated valves FAQ and common faults.
Capacitor Charge
When initially using Failsafe actuators, allow at least 30 seconds for the actuator to charge capacitor.
Will not move
Check power supply and wiring.
Will not return
Power Open/Close>> Check power supply
Failsafe return: Power the actuator for minimum 30 seconds to recharge the capacitors.
Which Wires Where
Check wiring diagram on side of actuator
Check wiring information on data sheet
Position Feed Back
These are volt free switches (no power supplied by actuator).
Check wiring diagram on side of actuator
Check wiring information on data sheet
Mounting
Horizontal or vertical (Not upside down, i.e. valve above motor actuator)
Actuator Spins 360 degrees or clicks and does not move
Internal micro switches are likely damaged.
If recently adjusted check cams are not loose. (Do not over tighten)
Other Questions, Call and ask us - we are always happy to help.