Water Solenoid Valves – Reliable Flow Control for Water Systems
At Solenoid Valve World, we offer a comprehensive range of high-performance water solenoid valves designed for precise, automatic control of water flow in residential, commercial, and industrial systems. Whether you're installing a new irrigation system, maintaining a water treatment plant, or automating a plumbing setup, our solenoid valves provide the durability and reliability you need.
What Is a Water Solenoid Valve?
A water solenoid valve is an electromechanical device that uses an electric coil to open or close a valve, allowing or stopping the flow of water. These valves are commonly used in:
Irrigation systems
Reverse osmosis systems
Plumbing automation
Water treatment facilities
HVAC and cooling systems
Key Features of Our Water Solenoid Valves
Available in 2/2 and 3/2 configurations
Normally closed, normally open or latching options
Compatible with cold and hot water applications
Body materials including brass, stainless steel, and plastic (nylon, PVC)
Internal seals available in EPDM, NBR, and FKM (Viton)
Wide range of sizes and connection types (BSP, NPT, compression, push-fit)
Why Choose Solenoid Valve World?
Global shipping and fast dispatch
Technical support for valve selection and installation
WRAS-approved valves for potable (drinking) water use
Operate with various voltages including 3v DC, 6V DC, 12V DC, 24V DC, 110V AC, 230V AC
Designed for low and high-pressure water systems, with options up to 30 bar+
Common Applications for Water Solenoid Valves
Our valves are trusted across a wide range of industries and uses:
Irrigation and sprinkler systems
Boiler and heating systems
Car wash equipment
Dishwashers and washing machines
Aquarium and hydroponics systems
Water softeners and purification units
Trusted Water Control – Every Time
With a wide selection of solenoid valves for water available in stock, Solenoid Valve World is your go-to source for affordable, reliable water control solutions. All valves are built for long-term durability, corrosion resistance, and leak-free operation.
Shop the full range of water solenoid valves now:
WRAS approved solenoid valves.
Plastic solenoid valves.
There are more specialist applications for pure, demineralised and Reverse Osmosis water systems where brass and copper must be avoided.
Mains water pressure is typically 3 to 4 Bar 45 to 60 psi where a Plastic solenoid valve is better suited, however is some instances mains water pressures can exceed 10 Bar for pumped systems or simply where the reservoir is very high in comparison to the outlet so a Brass WRAS solenoid valve would be better suited. Water pressure according to height is typically referred to as hydrostatic water pressure.
There are several factors to consider when choosing a solenoid valve to control water, pressure, temperature, flow, operation and function.
Pressure: Solenoid valves are rated according to a minimum and maximum pressure rating, be sure that your application is within these parameters to ensure the valve operates correctly and continues to function without the need for repeated repairs.
Temperature: Mains water will vary in temperature according to time of year between +5°C and +20°C, however some processing systems require hot water which is not ideally suited to plastic valves with NBR sealing which are typically restricted to +60°C, for higher temperature applications Brass bodied valves with EPDM sealing are better suited up to a maximum of +130°C. In some extreme cases pressures exceeding 100C a steam rated solenoid valve is better suited, with PTFE sealing and Class H or Class N high temperature coils suitable for temperatures up to +200°C.
Brass solenoid valves for high pressure water.
More information about solenoid coils can be found here.
Flow: Solenoid valves are supplied with a flow factor, typically Kv (measured as litres per minutes of water with 1 Bar pressure difference) or Cv (US Gallons per minutes with 1 psi pressure difference). Pressure difference also referred to as pressure differential which is the pressure difference between the inlet and outlet port of the valve. Flow will increase in direct proportion to the pressure difference between inlet and outlet port, i.e. the higher the pressure difference, the higher the flow. Read more about flow.
Typically, for general purpose applications a pressure drop of around 10% to 20% is the best practise, higher pressure differences will increase the speed of flow and can cause problems with water hammer when the valve suddenly closes.
Flow is calculated as Flow in litres per minute = Kv flow factor of the valve x square root (pressure difference divided by the density of the media).
Density of water = 1
Care must be taken when choosing a pressure assisted or hung diaphragm solenoid valve size, undersize can cause water hammer when closing due to fast moving water.
Remember water is heavy, 1 litre of water weighs 1 Kg, and stopping suddenly all that weight + energy has to go somewhere.
If a valve is too big, then the valve can open and close by itself as the pressure difference is not stable, in this case when the valve opens there is an immediate pressure drop at the inlet so the valve begins to close, this re-establishes the pressure difference required and so the valve will open again - this process repeats and you have a solenoid valve that bangs open and closed all be itself.
Operation: The operation of a solenoid valve can be Direct Acting, Assisted Lift or Pressure Assisted.
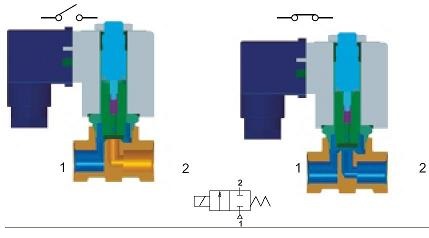
Direct Acting:
Water flow is controlled by the plunger resting over a seat, when lifted will allow flow and is not influenced by pressure changes and will operate from zero pressure difference up to its maximum working pressure. No system pressure difference is required to open or close the valve. Ideal for all pressure ranges, although typically low flow with smaller orifice (flow path) in comparison to other valve types below.
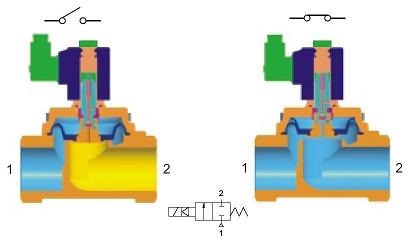
Hung Diaphragm:
a diaphragm is hung or attached to the plunger by means of a spring, which in turn covers a central internal pilot within the diaphragm. When the plunger lifts the diaphragm, it also reveals the internal pilot between the two which can aid the diaphragm lift and opening when pressure difference is available. When the valve closes the plunger covers the pilot so any pressure difference aids closing and the diaphragm returns to its seated position - closed. Ideally suited for suction and low pressure systems up to 10 Bar and offer good flow. Larger valve sizes above 1 inch can be more expensive and consume more electrical power.

Pressure Assisted:
a pressure assisted also known as servo or pilot assist and floating diaphragm valve is designed to utilise only the pressure difference, which must be guaranteed and is typically 0.5 Bar or 7 psi i.e. 0.5 Bar higher inlet pressure than outlet pressure. In this instance the plunger is located away from the diaphragm and when lifted releases the pressure above the diaphragm down stream so that the higher inlet pressure can lift the seal and open the valve. This design is a good solution for larger pipe systems above 1 inch, and typically offers a cost saving against direct acting or hung diaphragm valves for these sizes, they are ideally suited for open-ended systems such as water tank refill systems and can offer reduced power requirements as the coil does not need to lift a diaphragm and are commonly found on larger 1/2 and bigger high pressure solenoid valves.
Function: the function of a solenoid valve is typically given as the number of ports and its fail-safe (non energised) position. Typically, in the water control market a 2/2 way normally closed solenoid valve is by far the most popular, in this instance 2/2 way denotes 2 ports (inlet and outlet) with 2 positions (open or closed) with fail-safe position as closed or no flow when electrical power removed.
See valves with WRAS approval.
WRAS Approved Valves: for mains water applications that fully conform to the water regulations with all non-metallic components in contact with the water conforming to BS 6920 (Test for water quality) and have passed the vigorous testing of 200,000 open / closed cycles at maximum pressure and temperature and then a final 150% over pressure leak and temperature test.